Case Study: 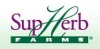
Using RFID To Insure Quality
Background
SupHerb Farms is a grower, processor and marketer of culinary herbs and specialty products. As such, maintaining a high standard of product quality and safety is a primary objective. To achieve this objective requires the ability to track raw materials from the harvest to final pack out. While manual procedures were already in use, they wanted to improve overall productivity and accuracy through automation. They called upon Marymonte Systems to analyze their needs and to suggest a solution that would take advantage of the current state of technology.
Opportunities and Objectives
- Monitor And Improve Raw Material Handing Procedures
- Quantify and measure all phases of raw material handling from field harvest to finished goods packaging
- Correlate the raw material handling process to QC sampling results
- Maximize quality through continuous improvement of raw material handling practices
- Increase overall productivity of raw material handling
- Insure Food Safety
- Correlate QC trends with specific harvest fields and raw material handling processes
- Provide complete traceability from finished goods back to date, time and field of harvest
The Solution
Applying RFID Tag To Each Trailer
The process begins by applying an RFID tag mounted in a watertight case to the side of each trailer. The tags are bolted to the trailer frame and are designed to survive harsh weather conditions. Once painted the tags are nearly invisible. Unlike barcodes, the RFID tag is not affected by dirt nor susceptible to incidental damage. Each tag is programmed with a an ID identifying the specific load (in this case, 404). This allows each load of product to be monitored as it arrives at the final transfer to production.
Automatically Tracking Raw Material
From Point Of Harvest....
As trailers of product are received at the plant, detailed data is collected about the point of harvest. In addition to the specific farm, field and cut, the system also tracks the date and time the harvest was started, when the harvest was completed and when the trailer left the field. This provides valuable insight into the overall harvesting and transportation process.
To The Processing Plant....
Once trailers of product are received at the plant, they are monitored as they are unloaded into processing. As the loads are brought to the unloading point, they pass by a fixed mount RFID reader station. The RFID tags are automatically read to identify the next load to be dumped. Once a load has been dumped, the system also tracks its final tare weight. Thus the exact net weight of the raw materials is obtained. At this point, the tracking of the raw material handling is complete and the next phase of tracking begins.
The reader and antenna are housed in a harsh-environment proof box to survive all weather conditions. The equipment selected by Marymonte Systems is capable of scanning the RFID tags through the closed box door and across a range of several feet.
Through Finished Goods Packaging....
Once the raw materials have been dumped, the system begins tracking its progress to finished goods packaging. Real time sensors monitor the movement of the product and track the specific processing path taken. Each load of raw materials is thus related to specific finished goods lot codes.
Each load is also correlated to specific QC sampling data based on the QC sampling date/time stamp and the real time tracking of the load by the system. Key micro data is automatically imported from the QC database and related to specific loads.
Mission Accomplished:
Quality and Full Traceability
Using RFID technology, SupHerb Farms now has the information they require to meet their objectives of high quality and food safety.
- Identifying Areas Of Raw Material Handling Improvements
-
- post production analysis correlating raw material handling procedures and QC results identify areas of possible improvement
- real time monitoring of raw material handling processes and taking corrective action early improves overall product quality
-
Product Safety Through Full Traceability - automating the data collection from field harvest to finished goods packaging provides true and complete traceability. SupHerb Farms' customers can be assured of the safety of their product
- Key Management Data - as a bonus, key management data is also available
- Product Yield Analysis - using raw material and finished goods weights, overall yields are easily computed
- Productivity And Capacity Studies - tons of raw material processed by shift, day, week, month, etc. provide valuable productivity and capacity information
- Farm/Field Performance - relating QC data to specific harvest points allows analysis of grower performance
-
Increased Accuracy and Higher Productivity - automating the data collection process not only reduces the amount of labor required but also increases the accuracy of the information collected
Contact Us today to see how your opportunities can become realities. (Phone 408-927-0606 or email sales@marymonte.com)